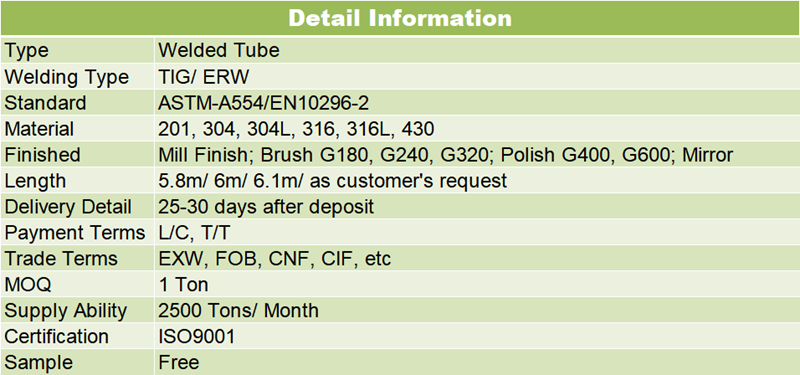
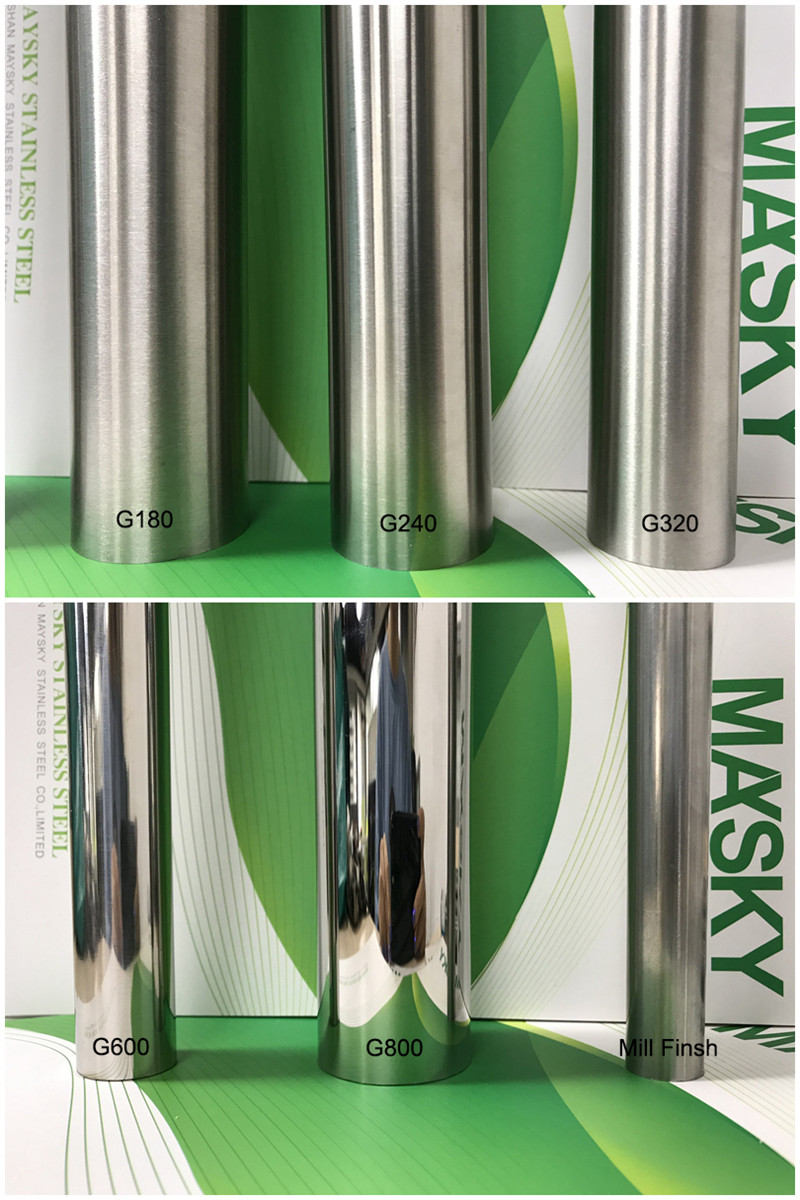
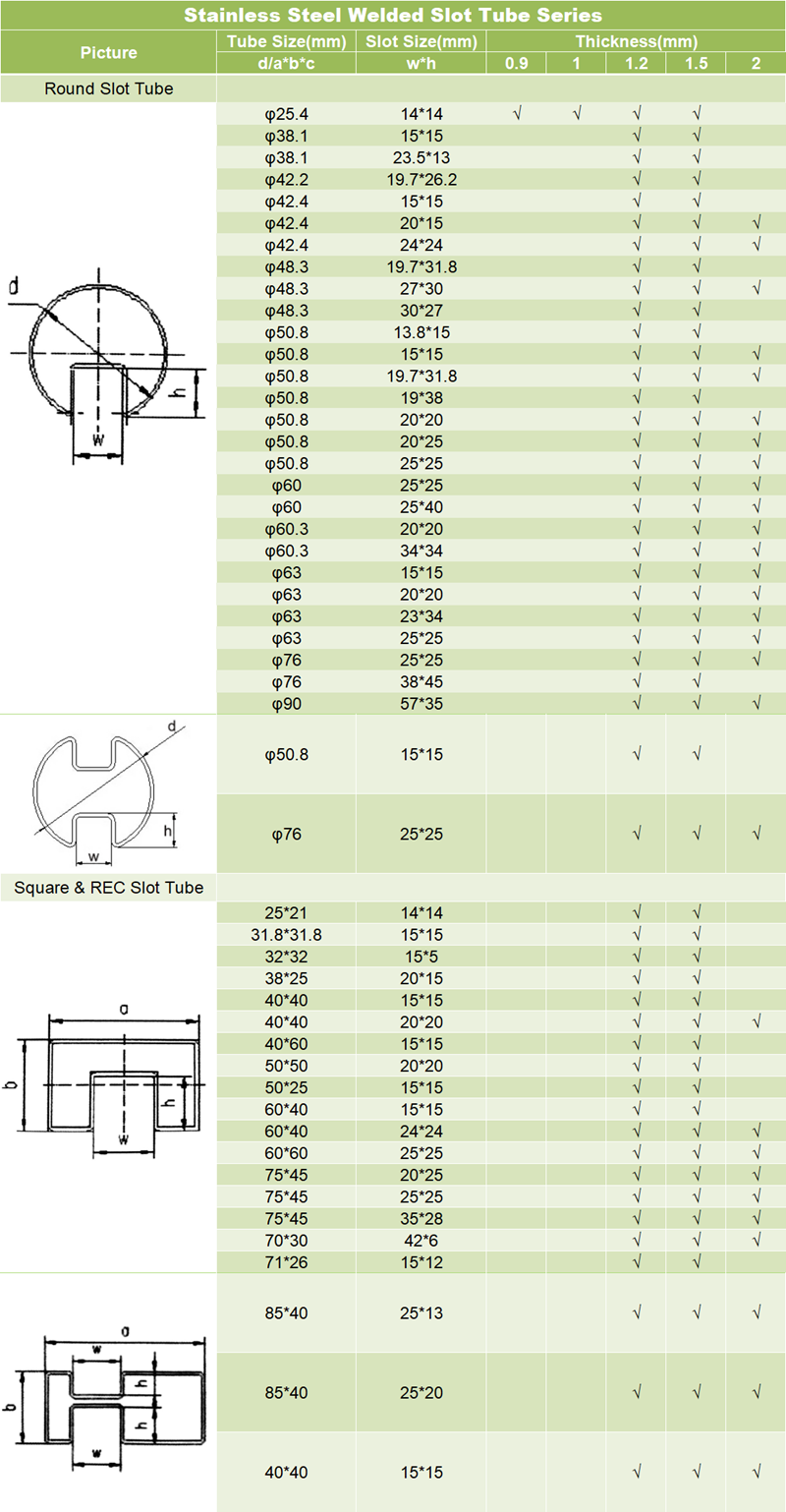
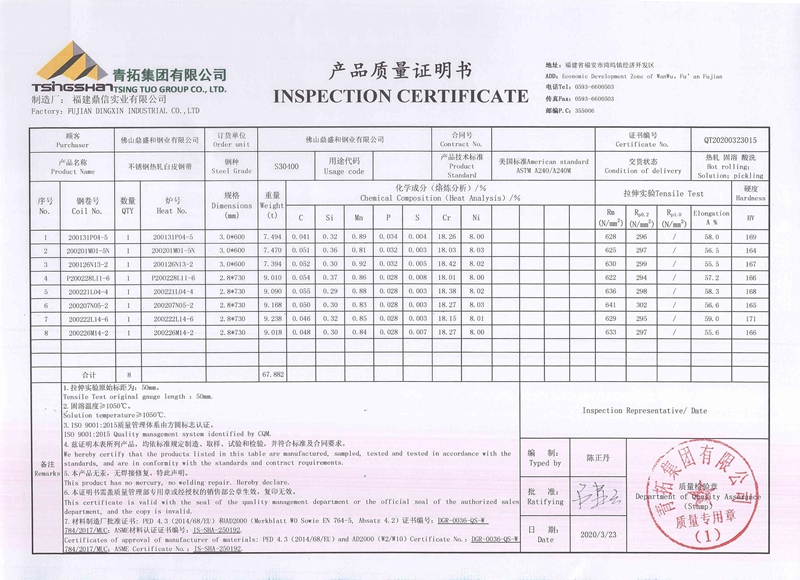
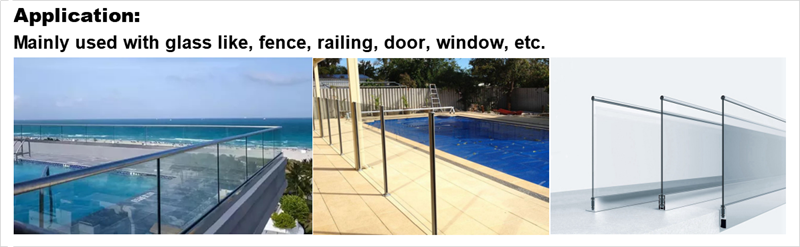
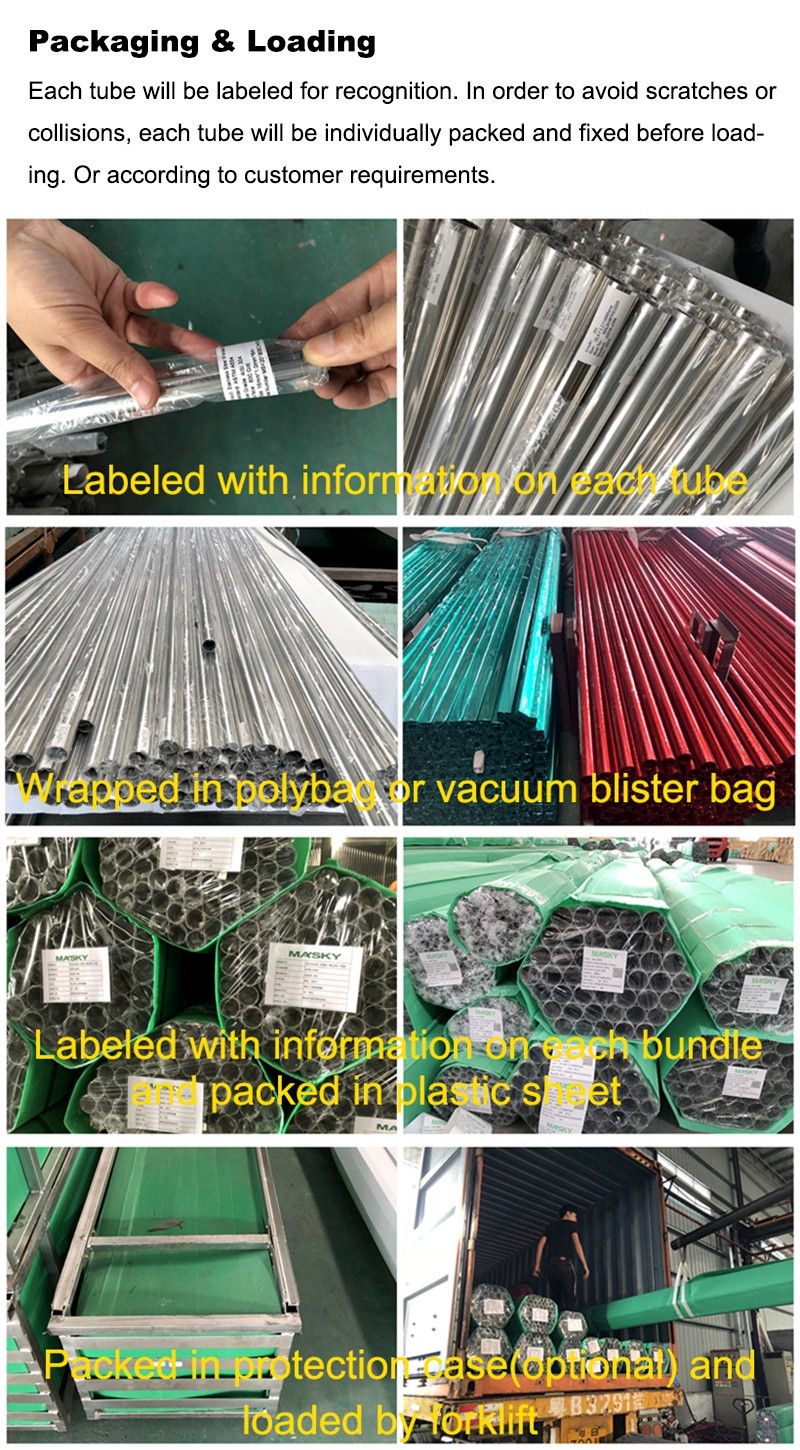
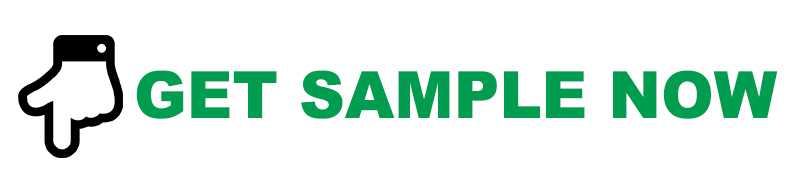
Slit burrs and sags/A batch of stainless steel slit rolls purchased by customers. During use, it was found that the edges were bent downwards, affecting the use, so the quality objection was raised. After measurement, the customer said that the edge curvature is formed by two parts, one is a burr and the other is a collapsed edge. Judging from the measurement results, the edge collapse phenomenon is more serious, and the amount of burr plus edge collapse reaches about 8 filaments. Collapse is generally caused by too much knife clearance during slitting. In addition, the elongation of the material is about large, and the amount of collapse is also greater. From the principle of shearing, sags and burrs always exist, but by reducing the amount of knife clearance, the sags and burrs can be controlled to a very small extent. However, if the blade clearance is too small, it will accelerate the wear of the props, so the blade clearance will always be controlled within an appropriate amount. This batch of materials is unqualified. It may be that the knife gap is set unreasonably when arranging the knife, or it may be due to insufficient pressure of the knife holder, or the props are excessively worn during processing. Considering that downtime is easy to cause uneven winding, in the general slitting process, the number of downtime inspections is minimized, which is also one of the reasons why the amount of edge collapse is not found to be too large. Because the amount of edge collapse is too large, the customer cannot use it. This batch of strips is recycled by the company, and the customer will be compensated.