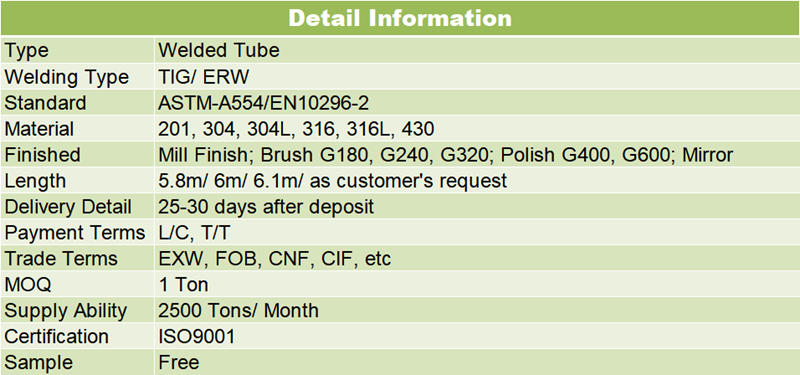
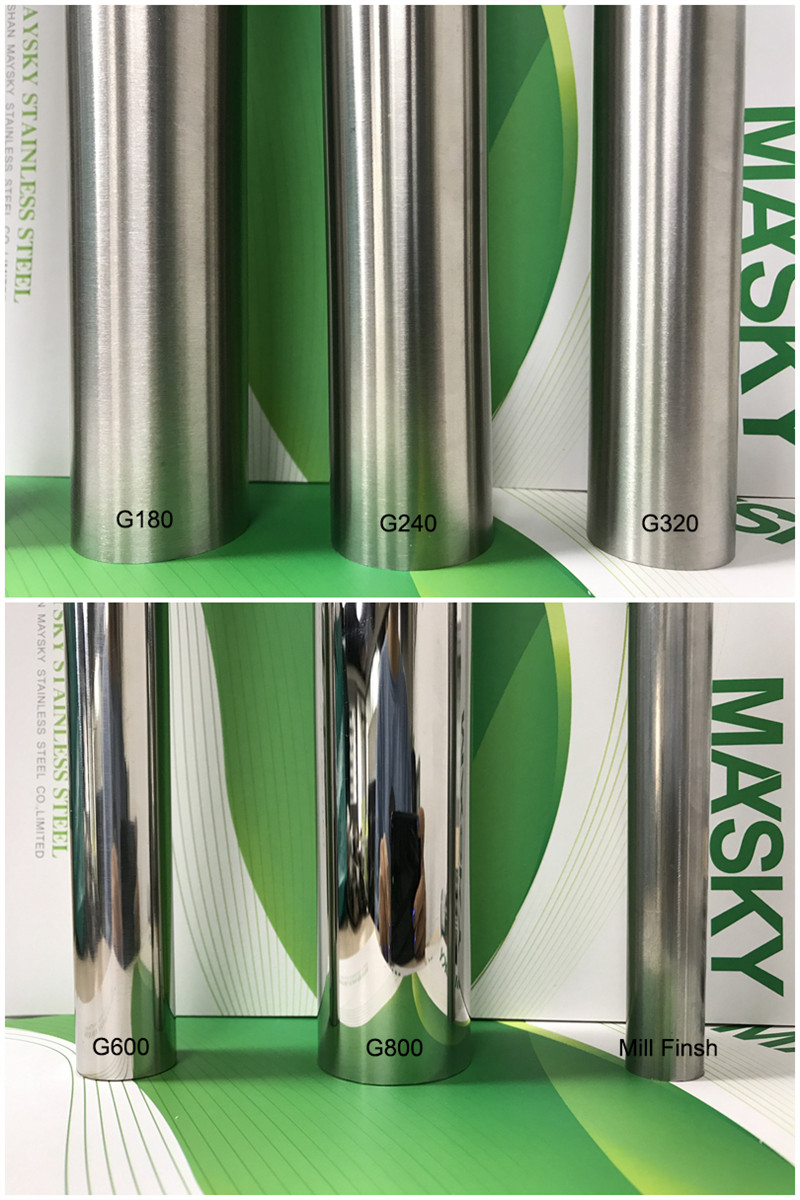
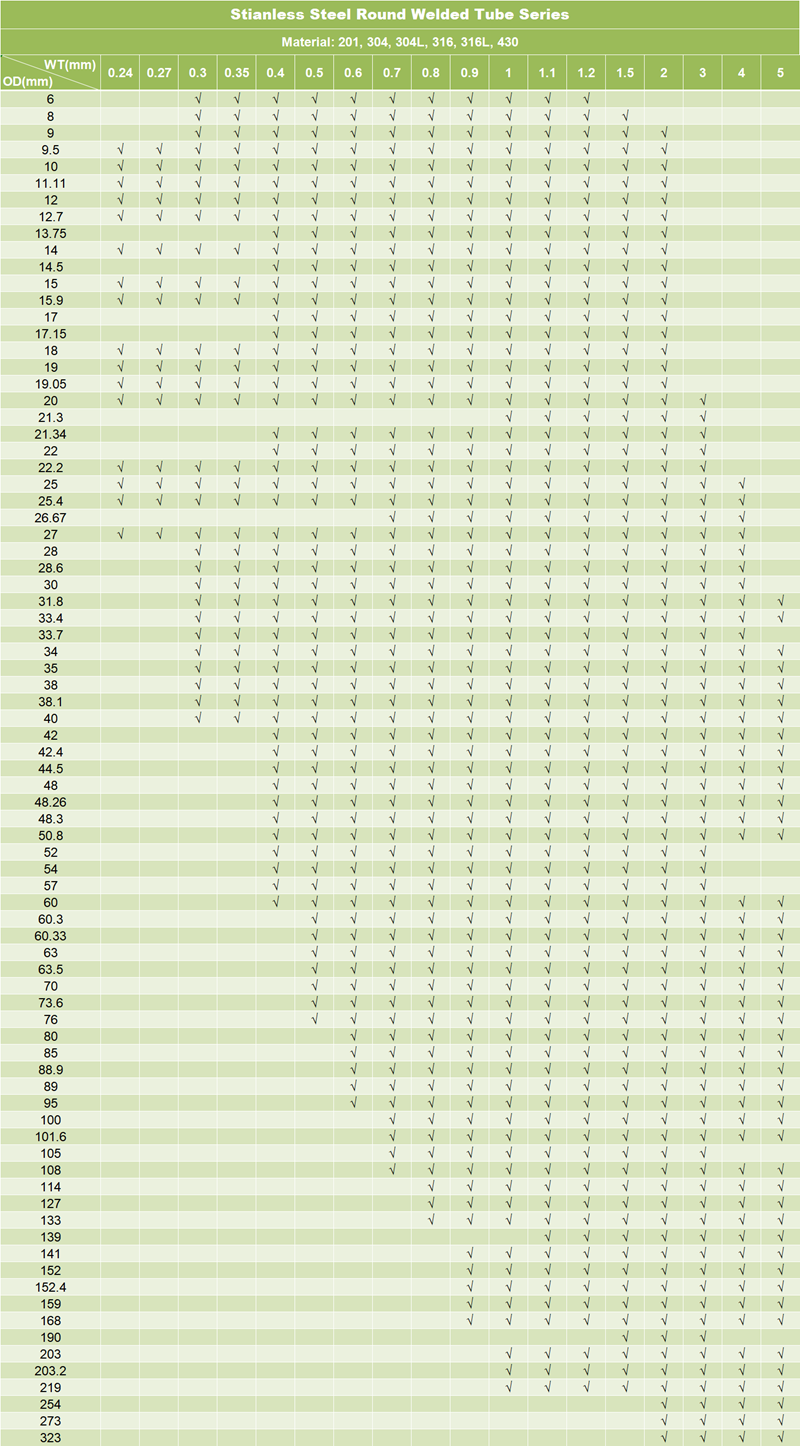
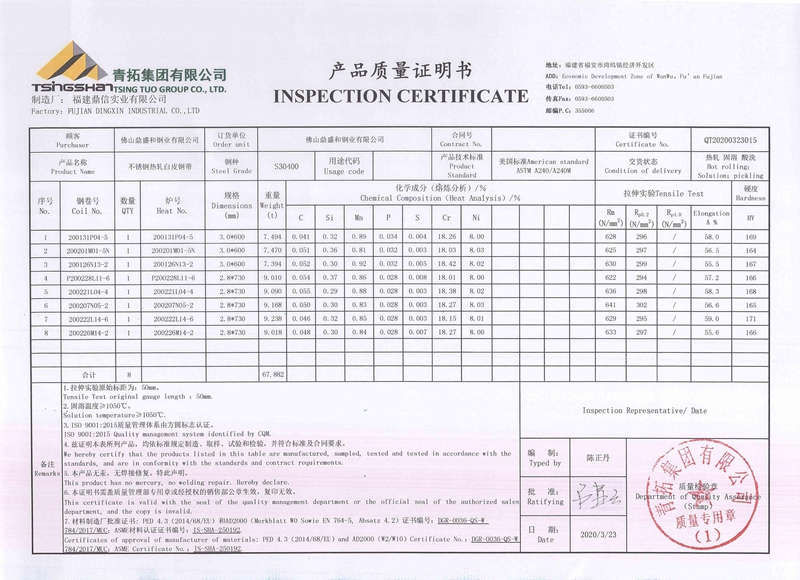
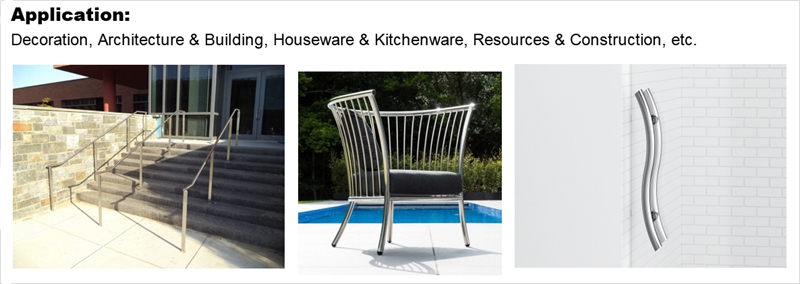
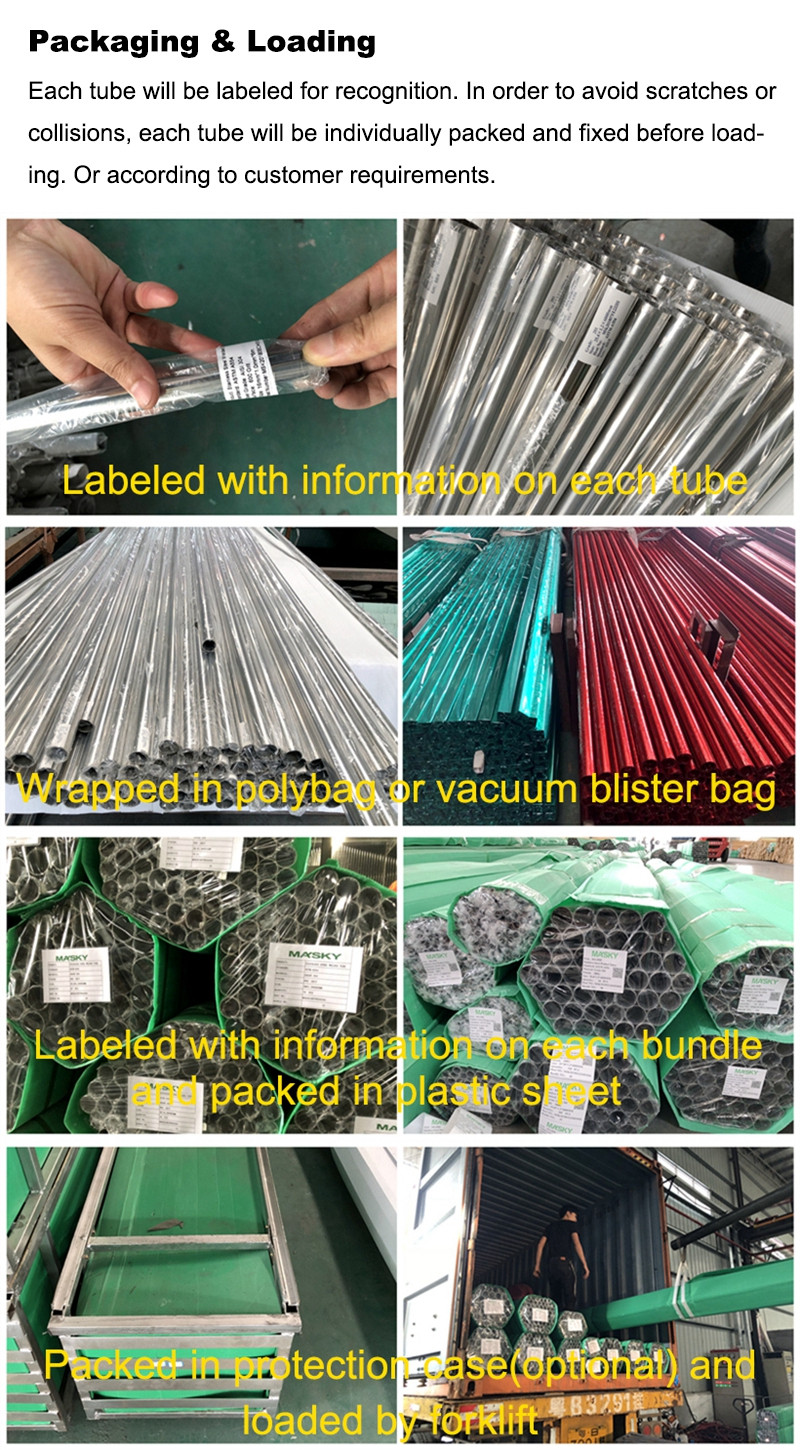
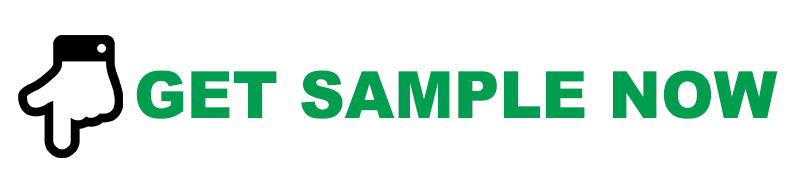
Scratches on the bottom of stainless steel coils/Customers complain that the back of a batch of stainless steel strips purchased is scratched, which is serious and affects their use. Therefore, it raises a quality objection. This batch of stainless steel slit rolls is made of 304/2B, with a thickness of 0.6mm and a width of 100mm. There are 10 strips in total, made of a 1219mm width stainless steel coil. After careful inspection, the scratches mentioned by the customer exist on the back of the steel coil, and the distribution is discontinuous, but the scratches are very dense, much like the friction between the board surface and a hard plane. Checking the processing records, I learned a very important message. The pressure is too large, and the knife shaft is not synchronized with the front pinch roller, which causes the processing to stop and readjust many times. When processing the steel coil, a large amount of adhesive tape was pasted on the rubber ring in order to solve the knife contamination, which resulted in an increase in the length of the steel coil of the slitting knife shaft portion. The knife shaft is not synchronized with the pinch roller, the knife shaft speed is slow, and the pinch roller speed is fast. The direct consequence is that there is a looper between the knife shaft and the pinch and the knife shaft and the transfer roller to buffer, the increased steel The rolls are all stacked in a looper. In the end, due to the excessive pushing of the steel coil, the sagging steel coil hits the bottom of the looper, and the steel coil is continuously transported, which causes friction between the steel coil and the bottom surface of the cement looper, causing a large number of scratches on the bottom surface of the steel coil. Due to the serious scratches, the scratched parts can only be scrapped. To deal with the knife, you can use a proper amount of tape, but it must not be too much, because too much tape will be used on the rubber ring, which will cause excessive friction of the entire knife shaft, and the pressure distribution of the knife shaft itself will be uneven. It is easy to cause all kinds of quality problems. To solve the dip knife, you can generally use a splint to make a set of splints, which is generally a necessary supporting facility for slitting equipment.