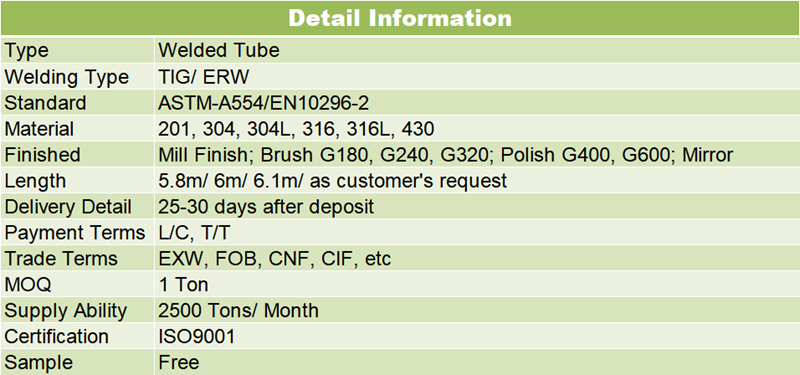
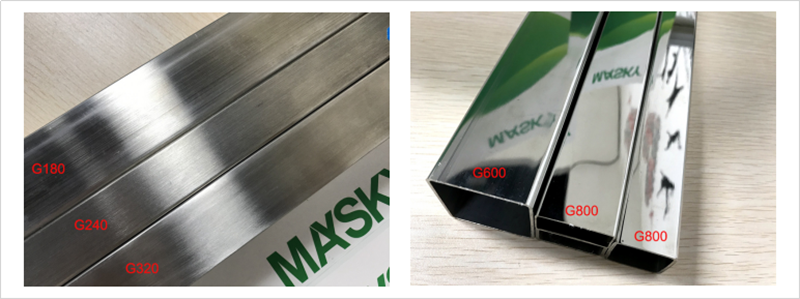
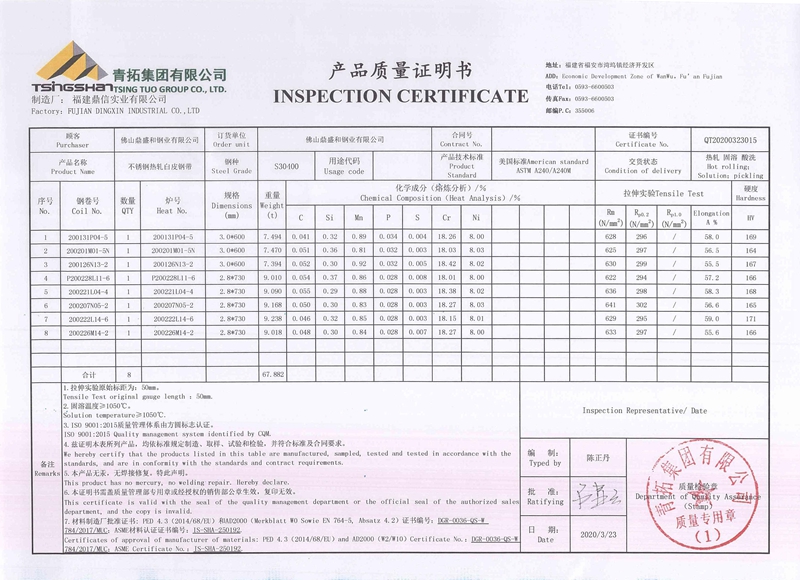
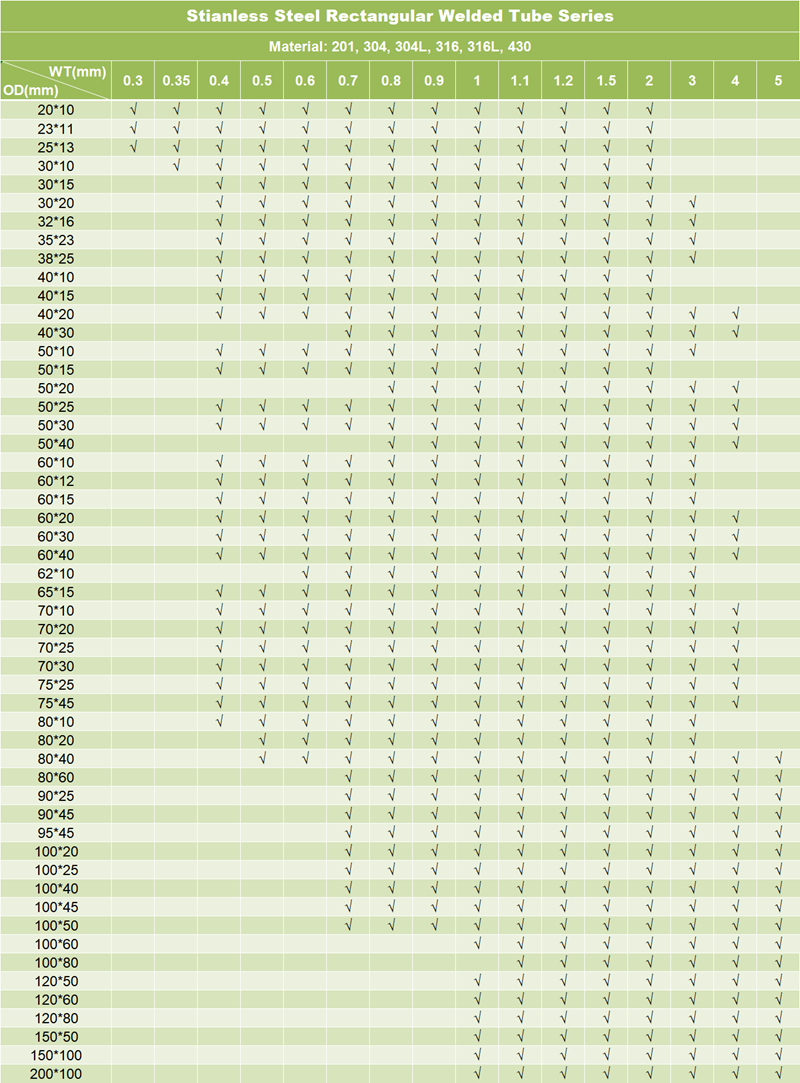
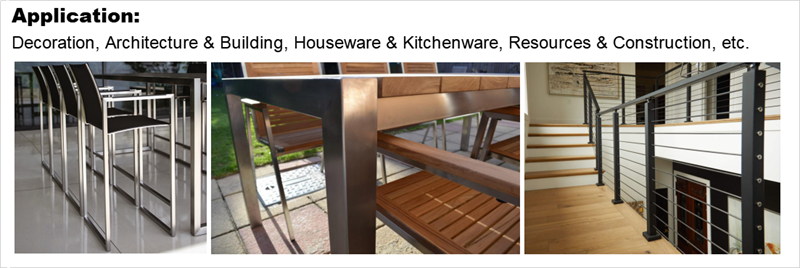
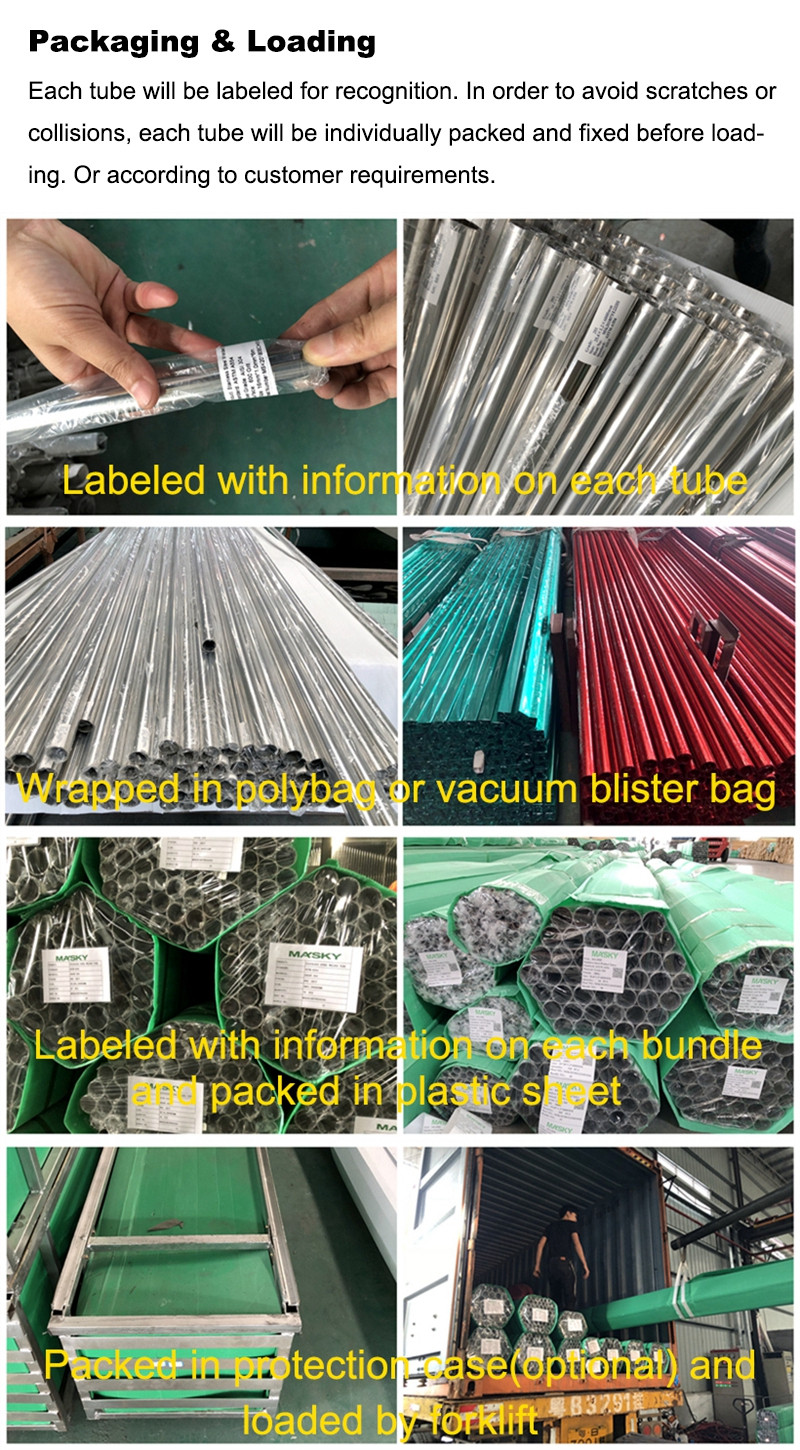
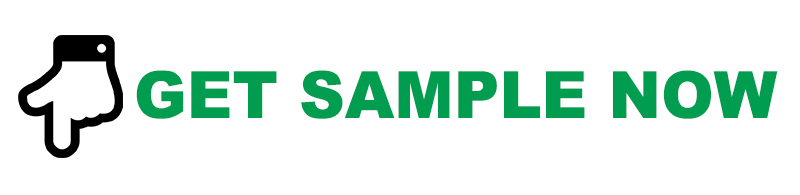
Impact of rolling oil life cycle on the surface of stainless steel cold-rolled/Customers are purchasing stainless steel hot-rolled N0.1 steel coils in a steel plant, and during the cold rolling process, they found that the surface is suspected of "pressing of iron scale", and proposed to the steel plant Complaints about quality objections. It is said that the purchased batch of strips has bright spots on the side, which affects the subsequent processing. On-site cold rolling production and physical observation: physical surface inspection was carried out on the user's production process and the suspected "iron scale pressing" after stainless steel cold rolling. For the user's production process and stainless steel physical surface observation, the rolling oil used by the user has been blackened Serious, dark brown in color. During the rolling process, the distribution of impurity particles in the rolling oil sticks to the surface of the rolled piece, making the surface of the strip steel after rolling not bright, and the degreasing process is difficult to eliminate. In addition, a black serpentine band will appear on the surface of the cold-rolled steel coil during a long storage period, which directly affects the product quality of the terminal. Take rolling oil analysis: dark brown rolling oil has poor oxidation resistance, high sulfur content, poor corrosion resistance, and high viscosity, which affects the surface finish of the strip. Obtaining high-quality cold-rolled stainless steel surface is eternal for each cold-rolling and rolling mill The pursuit of goals. Although the hot-rolled stainless steel strip is produced in the cold rolling process of reversible or irreversible rolling mills, each rolling pass is not the end surface of the finished product. But for stainless steel, the intermediate link in the rolling process directly affects the surface of the final product. At present, different types of cold rolling mills in my country generally adopt the rolling oil, emulsion, water rolling + oil drop mode. Rolling oil is generally composed of animal and vegetable fats + synthetic fat + special additives, and the commonly used concentration of emulsion is 5%. The use of rolling oil and emulsion is mainly determined according to the material and production process. Rolling stainless steel with rolling oil can reduce the friction coefficient and friction force on the arc surface of the contact area between the rolled part and the roll deformation zone. In high-speed rolling, it can reduce the wear of the rolls, ③ play the role of lubrication and cooling of the rolled parts. Both rolling oil and emulsion have the same function as lubrication and cooling. The difference is that emulsion is a small mixture of oil, its cooling effect is stronger, and the lubrication effect is relatively poor. The use of rolling oil cannot be blindly pursued for low cost. Adding appropriate synthetic esters in proper use can improve the lubricating properties of rolling oil. Adding phosphorus-containing compounds can improve the compressive and anti-wear properties of the rolling oil, and adding anti-corrosion agents can improve the protection ability of the rolling oil on the surface of the strip steel. If the pickling solution and passivation solution cannot remove grease, the grease present on the surface will also directly affect the pickling passivation surface. 2. The surface quality issue is not the responsibility of the steel mill and does not accept quality objections.